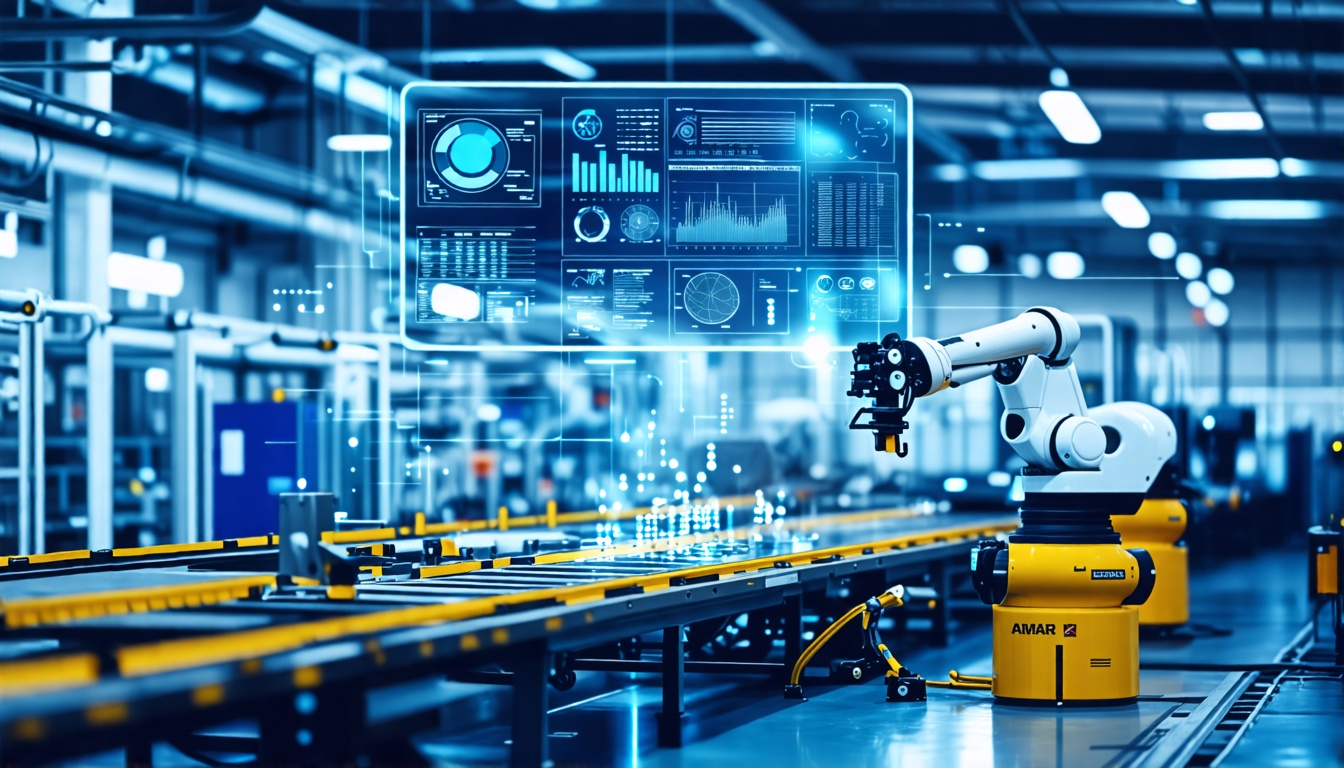
Introduction: AI x Quality
With the emergence of large language models (LLMs), in the public eye, the artificial intelligence (AI) hype cycle has reached new heights. It seems like everyone—from tech giants like Microsoft to cultural icons like The Beatles—is eager to join the AI revolution.
However, it’s important to remember that AI has been evolving for decades, with significant advancements long before the advent of ChatGPT and similar technologies. To distinguish between hype and reality, let’s explore some practical applications of AI in manufacturing, particularly in quality control (QC).
Unlike LLMs, whose future is still uncertain, AI in quality control has already demonstrated its effectiveness, with many more applications on the horizon. The impact on the manufacturing workforce is yet to be fully understood, but it’s undoubtedly an exciting time to be involved in quality control.
The traditional quality control methods
Quality control (QC) is essential for ensuring that the manufactured products meet specified standards and are free from defects. Traditional QC methods have been the backbone of manufacturing for decades. Here are some key traditional quality control methods:
1. Inspections: Visual and dimensional inspection which involves examining products visually using tools like callipers or micrometers to identify defects. It can be done at various stages of production, but it is crucial to ensure the product meets quality standards before reaching the customer.
2. Statistical Process Control (SPC): Control Charts are used to monitor the stability of manufacturing processes over time. By plotting data points on a chart, manufacturers can identify trends and variations that may indicate problems. And histograms show the distribution of data points, helping to identify patterns and deviations from the norm.
3. Sampling: Instead of inspecting every item, a random sample of products is tested. If the sample meets quality standards, the entire batch is accepted.
4. Destructive Testing: This involves testing products to the point of failure to understand their limits and ensure they meet safety standards.
5. Non-Destructive Testing (NDT): Techniques like X-rays, ultrasonic testing, and magnetic particle testing are used to detect internal defects without damaging the product.
6. Documentation and Standardization: Standard Operating Procedures (SOPs) are detailed written instructions on how to perform tasks correctly to ensure consistency and quality.
7. Root Cause Analysis: Identifying the underlying causes of defects and implementing corrective actions to prevent recurrence.
These traditional methods form the foundation of quality control in manufacturing, ensuring that products are consistently produced to meet customer expectations and regulatory requirements.
Traditional Methods vs. AI Integration
Traditional quality inspections in the manufacturing sector have predominantly depended on human intervention, with inspectors manually examining each product for defects, errors, or inconsistencies. While this approach has its advantages, it also presents several drawbacks. Manual inspections are often time-consuming, susceptible to human error, and lack the scalability needed for large-scale manufacturing operations.
In contrast, the integration of AI in quality inspections addresses these challenges effectively. AI-powered systems, including machine learning algorithms and computer vision, can analyse and inspect products much more rapidly and with greater precision than human inspectors. These systems can be trained to detect even the smallest anomalies, ensuring a higher level of accuracy and consistency in the inspection process.
An introduction to AI technologies used in quality control
In the rapidly evolving manufacturing industry, maintaining high product quality is crucial. Defective products can result in significant financial losses, damage to a company’s reputation, and diminish customer trust. This is where Artificial Intelligence (AI) and Machine Learning(ML) come into play, transforming quality control processes and driving manufacturing towards enhanced efficiency and precision.
1. Machine Learning (ML): Machine Learning algorithms analyse historical data to predict potential defects and failures before they occur. This proactive approach helps in reducing downtime and improving product quality. By learning from vast amounts of data, ML models can also identify patterns and detect anomalies that might indicate deviations from quality standards.
2. Automated Visual Inspection: Computer vision systems use cameras and image processing algorithms to inspect products for defects. These systems can detect surface defects, misalignments, and other visual inconsistencies with high precision. It also enables real-time monitoring of production lines, ensuring that any defects are detected and addressed immediately.
3. Natural Language Processing (NLP): NLP can automate the analysis of quality reports and documentation, extracting relevant information and identifying trends or recurring issues.
4. Robotic Process Automation (RPA): RPA can automate repetitive QC tasks, such as sorting and testing, reducing human error and increasing efficiency.
5. Data Analytics: AI-powered data analytics tools can process and analyse large datasets to uncover insights and trends that inform Quality Control processes. These tools enable real-time analysis of production data, allowing for immediate adjustments and improvements in quality.
6. Internet of Things (IoT): IoT devices collect data from various points in the production process, providing a comprehensive view of the manufacturing environment. These sensors monitor equipment health and predict maintenance needs, preventing unexpected breakdowns and ensuring consistent quality.
The future of quality control hinges on the seamless integration of AI and machine vision technologies. As AI algorithms advance, they will be capable of detecting even the most subtle defects that might currently go unnoticed. This will lead to enhanced product quality and increased customer satisfaction. Furthermore, AI’s capacity to learn from data ensures that the accuracy and efficiency of quality control processes will continually improve over time.
Benefits of AI-driven quality control
The integration of AI in quality control offers numerous advantages to the manufacturing industry. By automating processes, AI can enhance efficiency and productivity.
1. Fast Identification of Defect: With the help of computer vision and deep learning, AI-powered systems can swiftly identify defects anywhere along the production line monitored by cameras and sensors. AI-based solutions can increase defect detection rates by up to 90% compared to human inspections.
2. Precise Defect Root-Cause Analysis: AI-powered solutions not only detect defects but also identify their root causes. If multiple failures occur, AI can track their pattern to identify key focus areas that drive the failures. This helps prevent future defects by pinpointing areas in the value chain that need improvement, enabling engineers to continuously enhance yield and reduce defects.
3. Production Optimization: ML Algorithms can determine optimal operating conditions by analysing the vast history production data. It can automatically identify key variables for these conditions, thereby minimizing defects and product waste.
4. High Scalability and Easy Integration: AI systems can be easily deployed across multiple production sites, providing consistent performance and rapid adaptation to changes. They seamlessly integrate with existing tools and technologies, combining data from various sources to enhance predictions and insights. This real-time communication and information sharing between sites ensure that quality control measures are uniformly applied, leading to improved efficiency, consistency, and overall product quality.
5. Time Saving: AI engines can perform quality testing faster than humans and fully automate complex tasks. Automated quality testing requires lesser man-hours compared to manual testing, significantly saving time.
By leveraging AI in quality control, manufacturers can achieve higher efficiency, better product quality, and substantial cost savings, making it a transformative technology for the industry.
Challenges and limitations
Artificial Intelligence (AI) has revolutionized quality control in manufacturing, offering unprecedented precision and efficiency. However, the implementation of AI-driven systems is not without its challenges and limitations.
These are few issues that would provide a comprehensive understanding of the hurdles faced by manufacturers.
1. Data Collection and Quality: One of the primary challenges in AI-driven quality control is the need for high-quality data. AI algorithms rely on vast amounts of data to learn and make accurate predictions. However, collecting and maintaining high-quality data can be difficult as variations in data formats and sources can lead to inconsistencies that affect the performance of AI models.
2. Data Privacy and Security: Ensuring the privacy and security of sensitive manufacturing data is crucial, yet challenging.
3. Infrastructure and Integration: Implementing AI systems requires significant investment in infrastructure and integration with existing manufacturing processes. The cost of setting up AI infrastructure, including sensors, data storage, and computational resources, can be very expensive and prohibitive for many manufacturers. Also, many manufacturing facilities operate with legacy systems that are not easily compatible with modern AI technologies.
4. Workforce Adaptation: The transition to AI-driven quality control necessitates changes in the workforce. There is often a lack of skilled personnel who can develop, implement, and maintain AI systems. Existing employees may resist adopting new technologies due to fear of job displacement or lack of understanding.
5. Ethical and Regulatory Concerns: The use of AI in manufacturing raises several ethical and regulatory issues. AI algorithms can inadvertently perpetuate biases present in the training data, leading to unfair outcomes. Manufacturers must navigate a complex landscape of regulations governing the use of AI and data.
While AI-driven quality control offers significant benefits, it is essential to address these challenges and limitations to fully realize its potential.
Future trends and innovations
AI technology is continually advancing, with new algorithms and models being developed to enhance the effectiveness of AI-driven visual inspection and defect detection. A major advancement in AI technology is the development of deep learning algorithms. These sophisticated models can process vast amounts of data and recognize complex patterns, making them ideal for tasks defect detection and quality inspections.
As AI continues to evolve, its application in quality control within the manufacturing industry is set to undergo significant transformations. Future trends and innovations point towards shaping AI-driven quality control, enhancing efficiency, precision, and overall product quality.
1. Autonomous Quality Control Systems: One of the most promising trends is the development of fully autonomous quality control systems. These systems leverage advanced AI algorithms to perform real-time inspections and make decisions without human intervention. Self-Learning Capabilities – AI systems that continuously learn from new data to improve their accuracy and adapt to changes in manufacturing processes giving it the ability to detect defects and take corrective actions instantly, reducing downtime and waste.
2. Integration with IoT Devices: The integration of AI with the Internet of Things (IoT) is expected to create more interconnected and intelligent manufacturing environments where IoT devices provide real-time data from various stages of the production process, which AI can analyse to ensure consistent quality. It can use data from IoT devices to optimize production parameters and maintain high-quality standards.
3. Collaborative Robots (Cobots): Cobots are designed to work alongside human workers, enhancing productivity and safety. Improved sensors and AI algorithms can enable Cobots to perform complex quality control tasks with high precision. They can have more flexibility and adaptability easily switching between different tasks in various production environments.
4. Generative AI: Generative AI is emerging as a powerful tool for quality control, particularly in product design and process optimization. Generative AI can be used to create optimized product designs that meet quality standards while reducing material usage and production costs. Gen AI can also aid in simulating different production scenarios to identify the most efficient and effective processes.
5. Ethical and Sustainable AI: As AI becomes more prevalent in manufacturing, there is a growing emphasis on ethical and sustainable practices. Developing AI algorithms that are transparent and free from biases to ensure fair and accurate quality assessments. AI can also be used to optimize the production process to minimize waste and energy consumption, contributing to more sustainable manufacturing practices.
The future of AI-driven quality control in manufacturing is bright, with numerous innovations set to enhance efficiency, precision, and sustainability. By staying abreast of these trends, manufacturers can leverage AI to achieve higher quality standards and maintain a competitive edge in the market.
Conclusion
The integration of AI in quality control has ushered in a new era of precision, efficiency, and innovation in manufacturing. From traditional methods to advanced AI-driven systems, the journey has been transformative, addressing long-standing challenges and setting new benchmarks for quality standards. AI technologies such as machine learning, computer vision, and predictive analytics have not only enhanced defect detection and root-cause analysis but also optimized production processes, leading to significant cost savings and improved product quality.
As we look to the future, the potential of AI in quality control continues to expand. Autonomous quality control systems, enhanced predictive analytics, and the integration of AI with IoT devices promise to create more intelligent and interconnected manufacturing environments. Collaborative robots and Generative AI will further revolutionize the industry, offering unprecedented flexibility and efficiency. Moreover, the emphasis on ethical and sustainable AI practices will ensure that these advancements contribute to a more responsible and eco-friendly manufacturing landscape.
In conclusion, the future of AI-driven quality control is bright, with continuous innovations poised to redefine the manufacturing industry. By embracing these technologies, manufacturers can achieve higher quality standards, reduce operational costs, and maintain a competitive edge in the global market. The journey of AI in quality control is just beginning, and its potential to drive excellence and sustainability in manufacturing is boundless.